Lembro até hoje do momento em que segurei meu primeiro manômetro digital nas mãos. Era um técnico iniciante, trabalhando em uma oficina mecânica pequena, e sempre batalhava com aqueles medidores antigos de ponteiro que pareciam ter vida própria. Cada medição era uma aventura – ora marcava uma coisa, ora outra completamente diferente.
Foi quando meu supervisor me entregou aquele pequeno aparelho digital e disse: “Experimenta isso aqui”. Naquele momento, não imaginava que estava conhecendo uma tecnologia que revolucionaria não só meu trabalho, mas toda a forma como medimos pressão no mundo moderno.
Por que o manômetro digital transformou a medição de pressão
A medição precisa de pressão sempre foi um desafio para profissionais de diversas áreas. Antes dos equipamentos digitais, dependíamos exclusivamente de instrumentos analógicos que, apesar de funcionais, apresentavam limitações significativas.
O manômetro digital surgiu como resposta a essas necessidades, oferecendo precisão, facilidade de uso e recursos que eram impensáveis na era analógica.
Este equipamento utiliza sensores eletrônicos para detectar variações de pressão e converte essas informações em dados digitais apresentados em um display. Diferente dos modelos tradicionais que dependem de mecanismos mecânicos, o medidor digital oferece leituras instantâneas e extremamente precisas.
Como funciona um medidor de pressão digital
O funcionamento do manômetro digital baseia-se em tecnologia de sensores piezorresistivos ou capacitivos. Quando a pressão é aplicada ao sensor, ocorrem mudanças nas propriedades elétricas dos materiais, que são interpretadas por um microprocessador interno. Este processamento converte os sinais elétricos em valores numéricos apresentados no display.
Os componentes principais incluem o sensor de pressão, circuito eletrônico de processamento, display digital e sistema de alimentação. Cada elemento trabalha em conjunto para garantir medições confiáveis e repetitivas.
Tipos de tecnologia utilizados
Existem diferentes tecnologias empregadas nos medidores digitais. Os sensores piezorresistivos utilizam materiais que alteram sua resistência elétrica sob pressão. Já os capacitivos baseiam-se na variação da capacitância quando submetidos a diferentes pressões. Ambas as tecnologias oferecem alta precisão, mas podem ser mais adequadas para aplicações específicas.
Vantagens incomparáveis dos equipamentos digitais
A precisão é talvez a maior vantagem do manômetro digital. Enquanto instrumentos analógicos podem apresentar erros de leitura devido a paralaxe, desgaste mecânico ou calibração inadequada, os digitais mantêm consistência nas medições. A margem de erro típica varia entre 0,1% a 0,5% da escala total, muito superior aos analógicos.
A facilidade de leitura representa outro benefício significativo. O display digital elimina interpretações duvidosas de ponteiros, fornecendo valores exatos. Muitos modelos oferecem retroiluminação, permitindo uso em ambientes com pouca luz.
Recursos avançados disponíveis
Os medidores digitais modernos incorporam funcionalidades que vão muito além da simples medição. Recursos como memória para armazenar leituras anteriores, conectividade bluetooth para transferência de dados, alarmes programáveis e compensação automática de temperatura elevam significativamente a utilidade desses equipamentos.
Aplicações práticas em diferentes setores
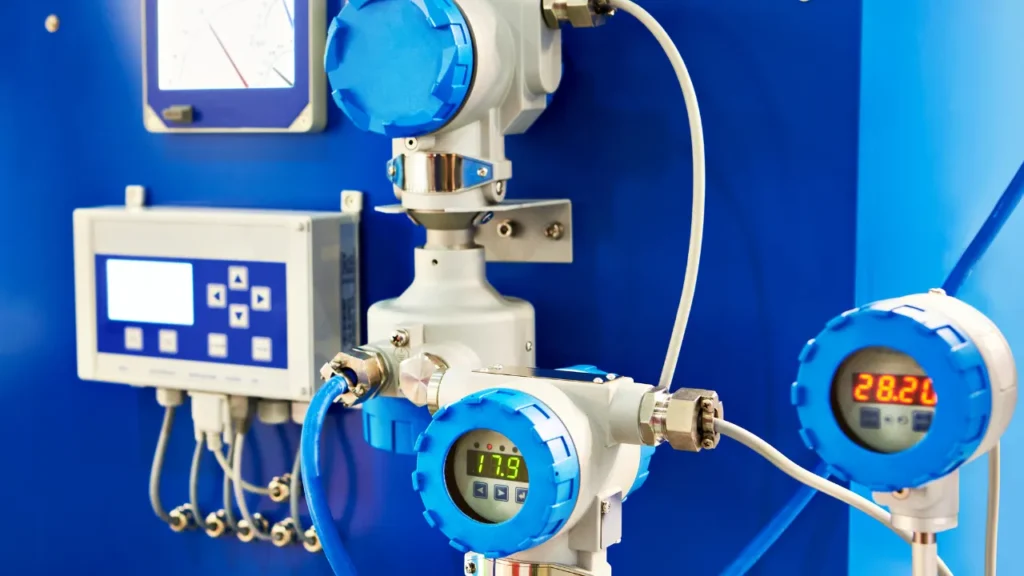
O manômetro digital encontra aplicação em praticamente todos os setores industriais. Na manutenção automotiva, permite verificar pressão de pneus, sistemas hidráulicos e pneumáticos com precisão milimétrica. Técnicos relatam economia de tempo significativa nas inspeções rotineiras.
Na indústria, o controle de processos exige medições confiáveis. Sistemas de ar comprimido, circuitos hidráulicos e equipamentos pressurizados dependem de monitoramento constante. O medidor digital oferece a confiabilidade necessária para manter operações seguras e eficientes.
Setor médico e laboratorial
Equipamentos médicos frequentemente requerem controle preciso de pressão. Ventiladores pulmonares, equipamentos de diálise e sistemas de infusão dependem de medições exatas para funcionamento seguro. O manômetro digital garante a precisão necessária para aplicações onde vidas estão em jogo.
Em laboratórios, experimentos científicos exigem controle rigoroso de variáveis. A pressão é frequentemente um parâmetro crítico que deve ser monitorado com extrema precisão. Os medidores digitais atendem essa demanda com margem de erro mínima.
Escolhendo o equipamento ideal
A seleção do manômetro digital adequado depende de diversos fatores. A faixa de pressão necessária é o primeiro critério. Equipamentos estão disponíveis desde baixas pressões (mbar) até pressões extremamente altas (milhares de PSI). Escolher a faixa correta garante precisão máxima e vida útil prolongada.
A resolução do display também merece atenção. Para aplicações que exigem alta precisão, displays com maior número de dígitos decimais são essenciais. A unidade de medida deve ser compatível com os padrões utilizados no ambiente de trabalho.
Características técnicas importantes
A precisão especificada pelo fabricante indica a confiabilidade das medições. Valores típicos variam entre 0,1% e 1% da escala total. A temperatura de operação define em quais condições o equipamento mantém precisão. Modelos industriais suportam temperaturas extremas, enquanto versões básicas têm limitações.
A alimentação é outro aspecto crucial. Modelos com bateria oferecem portabilidade, mas requerem substituição periódica. Versões com alimentação externa são ideais para uso contínuo. Alguns equipamentos combinam ambas as opções.
Calibração e manutenção essenciais
A calibração periódica mantém a precisão do manômetro digital ao longo do tempo. Equipamentos de medição estão sujeitos a deriva, processo gradual onde as leituras se afastam dos valores reais. Calibração regular corrige essas variações, garantindo confiabilidade contínua.
A frequência de calibração depende da criticidade da aplicação e recomendações do fabricante. Ambientes industriais rigorosos podem exigir calibração trimestral, enquanto aplicações menos críticas permitem intervalos anuais.
Cuidados básicos de conservação
O armazenamento adequado prolonga a vida útil do equipamento. Locais secos, protegidos de temperaturas extremas e choques mecânicos preservam os componentes eletrônicos. Cases de proteção são investimentos valiosos para equipamentos portáteis.
A limpeza regular do display e conectores mantém a funcionalidade. Produtos específicos para eletrônicos devem ser utilizados, evitando danos aos componentes sensíveis.
Comparação com manômetros analógicos
Embora os medidores digitais ofereçam vantagens significativas, os analógicos ainda têm seu lugar. A principal vantagem dos analógicos é a independência de energia elétrica. Em ambientes onde a bateria pode descarregar ou não há alimentação disponível, os modelos mecânicos continuam funcionando.
O custo inicial dos analógicos é geralmente menor, tornando-os atrativos para aplicações básicas. Entretanto, quando consideramos precisão, facilidade de uso e recursos adicionais, o manômetro digital oferece melhor custo-benefício a longo prazo.
Durabilidade e resistência
Os equipamentos analógicos tradicionais são conhecidos pela robustez mecânica. Muitos suportam choques e vibrações que poderiam danificar eletrônicos sensíveis. Porém, medidores digitais modernos incorporam proteções que rivalizam com a durabilidade dos analógicos.
“A precisão é a mãe da confiança, e a confiança é a base de toda decisão técnica bem-sucedida” – Dr. Roberto Silva, engenheiro mecânico
Tendências tecnológicas futuras
A evolução dos medidores de pressão digitais aponta para maior integração com sistemas inteligentes. Internet das Coisas (IoT) permite monitoramento remoto em tempo real, transformando medição pontual em supervisão contínua. Esta conectividade revoluciona a manutenção preditiva e controle de processos.
Inteligência artificial começa a ser integrada aos equipamentos, permitindo análise automática de tendências e predição de falhas. Algoritmos aprendem padrões de comportamento dos sistemas monitorados, antecipando problemas antes que causem danos.
Miniaturização e eficiência energética
O desenvolvimento de sensores cada vez menores e mais eficientes permite criar manômetros digitais portáteis com autonomia estendida. Novas tecnologias de bateria e circuitos de baixo consumo prolongam significativamente o tempo de operação.
A miniaturização também facilita a integração em espaços reduzidos, expandindo as possibilidades de aplicação em equipamentos compactos.
Considerações de segurança
O uso adequado do manômetro digital envolve observar limites de pressão especificados pelo fabricante. Aplicar pressões superiores ao limite pode danificar permanentemente o sensor, comprometendo a precisão ou causando falha completa.
A proteção contra sobrepressão é essencial em aplicações críticas. Válvulas de alívio ou limitadores de pressão protegem o equipamento e garantem segurança operacional.
Protocolos de verificação
Estabelecer rotinas de verificação periódica identifica problemas antes que afetem as medições. Comparações com padrões conhecidos ou outros equipamentos calibrados revelam desvios que requerem atenção.
Documentar as verificações cria histórico valioso para análise de tendências e planejamento de manutenção.
Impacto econômico da tecnologia digital
A adoção de medidores digitais representa investimento inicial maior, mas os benefícios econômicos se manifestam rapidamente. A maior precisão reduz desperdícios em processos industriais, enquanto a confiabilidade diminui paradas não programadas.
A eficiência operacional melhora significativamente com leituras instantâneas e precisas. Técnicos executam mais verificações no mesmo tempo, aumentando a produtividade das equipes de manutenção.
Retorno do investimento
Estudos mostram que empresas que modernizaram seus sistemas de medição reportam economia média de 15% nos custos operacionais relacionados a controle de pressão. A redução de retrabalho e maior confiabilidade dos processos justificam rapidamente o investimento inicial.
Implementação em diferentes ambientes
A transição para manômetros digitais requer planejamento cuidadoso. Avaliar as necessidades específicas de cada aplicação orienta a seleção dos equipamentos mais adequados. Ambientes agressivos podem exigir proteções especiais ou modelos industriais reforçados.
O treinamento das equipes é fundamental para aproveitar todos os recursos disponíveis. Operadores familiarizados com equipamentos analógicos podem inicialmente resistir à mudança, mas rapidamente reconhecem as vantagens dos digitais.
Integração com sistemas existentes
Muitos medidores digitais modernos oferecem interfaces de comunicação que facilitam a integração com sistemas de supervisão existentes. Protocolos padrão como Modbus, RS-485 ou comunicação sem fio permitem centralizar o monitoramento de múltiplos pontos.
Esta integração transforma medições isoladas em sistemas inteligentes de supervisão, proporcionando visão abrangente dos processos monitorados.
Principais pontos sobre manômetros digitais:
- Precisão superior: Margem de erro entre 0,1% e 0,5%, muito maior que equipamentos analógicos
- Facilidade de leitura: Display digital elimina erros de interpretação de ponteiros
- Recursos avançados: Memória, conectividade, alarmes e compensação térmica
- Aplicação universal: Adequado para automotivo, industrial, médico e laboratorial
- Calibração essencial: Manutenção da precisão através de verificações periódicas
- Custo-benefício: Investimento inicial maior compensado por eficiência operacional
- Tecnologia em evolução: IoT e inteligência artificial expandem as possibilidades
- Segurança crítica: Respeitar limites de pressão e protocolos de verificação
- Impacto econômico positivo: Redução de desperdícios e aumento de produtividade
- Integração inteligente: Compatibilidade com sistemas de supervisão modernos
Perguntas frequentes sobre manômetros digitais
1. Qual a diferença de precisão entre manômetros digitais e analógicos? Manômetros digitais oferecem precisão de 0,1% a 0,5%, enquanto analógicos ficam entre 1% a 3% da escala total.
2. Com que frequência devo calibrar meu manômetro digital? Recomenda-se calibração anual para aplicações básicas e trimestral para uso industrial crítico.
3. Manômetros digitais funcionam sem bateria? Não, todos requerem alimentação elétrica, seja por bateria ou fonte externa, diferente dos analógicos mecânicos.
4. Posso usar manômetro digital em ambientes com alta umidade? Sim, modelos com proteção IP adequada suportam ambientes úmidos, mas verifique as especificações do fabricante.
5. Qual a vida útil típica de um manômetro digital? Com uso adequado e manutenção regular, podem durar 10-15 anos, similar aos analógicos de qualidade.
6. É possível conectar manômetros digitais ao computador? Muitos modelos modernos oferecem conectividade USB, Bluetooth ou interfaces industriais para transferência de dados.
7. Manômetros digitais são mais frágeis que os analógicos? Versões industriais possuem robustez comparável aos analógicos, mas modelos básicos podem ser mais sensíveis.
8. Qual a temperatura máxima de operação? Varia conforme o modelo, mas equipamentos industriais suportam tipicamente -20°C a +80°C.
9. Como identificar quando o manômetro precisa de calibração? Compare com padrão conhecido ou outro equipamento calibrado, verificando desvios superiores à precisão especificada.
10. Posso usar manômetro digital para gases corrosivos? Apenas modelos com materiais compatíveis e proteções adequadas, consultando sempre as especificações técnicas.